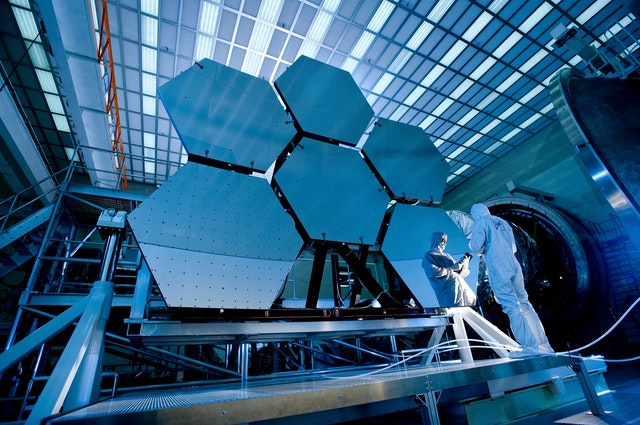
Continuous strengthening of skills, qualification improvement and retraining of employees will become one of the key challenges in the Lithuanian manufacturing sector during the Industry 4.0 revolution. This revolution will affect the movement of labour in all sectors of the manufacturing industry: some workers will lose their jobs, some will have to change or supplement their functions, and completely new professions will emerge, mainly related to the development and maintenance of new technologies. Such trends have been demonstrated by an analysis on the needs for competencies of small and medium-sized enterprises (SME) to prepare for and meet the challenges of Industry 4.0. The analysis was performed by Panevėžys Development Agency.
The analysis was commissioned by the European Social Fund Agency in the framework of the Interreg Europe-funded project “Capacity Building of Small and Medium-sized Enterprises in Preparation for Industry 4.0 (4.0 Ready)”.
The results of the analysis were presented on June 30th to the representatives of the Ministry of Economy and Innovation of the Republic of Lithuania, the Ministry of Education, Science and Sports of the Republic of Lithuania, vocational training, business, science and innovation organizations.
The aim of this analysis is to determine what competencies will be needed by SME employees working in the main Lithuanian industrial sectors (food, chemical, furniture, wood, machinery and equipment) over the next ten years to meet the challenges of Industry 4.0. At the same time, the aim was to find out the possible directions of movement of employees in the labour market, the essential need for future competencies according to the professional qualifications of employees, to evaluate retraining measures in Lithuania. The demand forecast for the main occupations of the Lithuanian industrial sectors (according to the Lithuanian Classification of Occupations) until 2030 was also made.
The results of the analysis will be used to develop a regional action plan with suggestions on how to improve EU funding instruments that can help SME prepare for Industry 4.0.
The analysis showed that continuous skills development, qualification improvement and retraining of employees will become one of the key challenges in the Lithuanian manufacturing sector during the Industry 4.0 revolution. This revolution will affect the movement of labour in all sectors of the manufacturing industry: some workers will lose their jobs, some will have to change or supplement their functions, and completely new professions will emerge, mainly related to the development and maintenance of new technologies.
The analysis found that so far only a very small proportion of employees (5%) could be completely replaced by robots and automated solutions, a much larger proportion of employees (60%) could be partially automated or complemented by innovative solutions. Technology will allow the manufacturing sector to move to a white-collar work. Fewer and fewer people will work in physical jobs and will not have to perform production tasks themselves, but only to supervise production processes, analyse data, ensure optimization of production processes, supervise cyber security of production. Technicians and operators who previously worked with and operated the equipment themselves will take over the work of engineers in the future, and engineers will not only develop products or organize production processes, but will also have to engage in communication with customers.
Due to Industry 4.0, in the next decade, all industrial sectors will reduce the need for workers to perform routine physical activities that are most easily automated. Demand for workers performing routine cognitive activities will fall by more than half. The need for employees who perform non-routine cognitive activities will not decrease or decrease insignificantly because the activities they perform cannot be or are difficult to automate or digitize. The need for workers performing non-routine physical activities will remain slightly lower than for workers performing non-routine cognitive activities.
The analysis identifies key competencies related to Industry 4.0 that will be relevant to all industrial sectors over the next decade, namely technical skills (especially relevant to low- and medium-skilled workers), the most important of which are:
– the knowledge / holistic understanding of the production process and procedures required for the performance of the process, as well as systematic knowledge, understanding and perception;
– data and IT skills (especially relevant to medium- and high-skilled workers), the most important of which are data evaluation and analysis skills and security and protection skills in the handling of sensitive data;
– social skills (especially relevant to medium- and high-skilled workers), the most important of which are cooperation, interpersonal, team and collaboration skills and communication competencies;
– personal skills that are relevant to all employees at the professional qualification level, i. e. continuous, independent learning / desire for lifelong learning, analytical thinking skills, interdisciplinary thinking, performance and problem solving.
The analysis indicates that the level of digitization and automation of processes in the Lithuanian food and beverage industry will not be very high due to the specifics of the sector. Over the next ten years, the demand for medium-skilled workers in the food and drink industry will decrease, the demand for high-skilled workers will increase and the demand for low-skilled workers will remain the same.
The majority of employees in the Lithuanian chemical product manufacturing sector are of medium and high qualification. Due to strong competition from foreign countries, investment in process digitization and automation in the chemicals’ and chemical products’ sector is not expected to decrease in the next decade, which will increase the need for highly qualified employees – mainly managers, legal professionals, engineers. The technological changes associated with Industry 4.0 will have the effect of reducing the number of mid-skilled workers as fewer laboratory technicians, equipment and machine operators will be needed.
Lithuanian wood industry sector will be affected differently by Industry 4.0 due to the specifics of different sectors: the most intensive level of digitization and automation will be in the production of furniture and paper, paper products, the lowest – in the wood processing industry sectors. However, the overall demand for workers in the wood industry will shrink over the next decade, most notably in the paper and paper products’ sector. The demand for medium-skilled workers will decrease the most, the number of low-skilled workers will remain low, and the demand for high-skilled workers will increase in the future.
Technological changes will reduce the number of employees in the Lithuanian machinery and equipment manufacturing sector, and will negatively affect medium and low-skilled workers. However, the successful transformation of production processes will require significantly more highly skilled workers, so the number of these skilled workers in the machinery and equipment manufacturing sector is expected to increase over the next decade.
Retraining measures in Lithuania
Three ministries in Lithuania – the Ministry of Education, Science and Sports, the Ministry of Economy and Innovation and the Ministry of Social Security and Labour – are responsible for the development of competencies required for adult continuing education, retraining and the labour market in Lithuania. The analysis notes that different ministries focus on different areas of activity, so there is a lack of a common holistic interdepartmental approach to the formation of human resources that meet future needs and the provision of the necessary competencies and qualifications. In order to develop and implement appropriate retraining measures, more effective cooperation between all ministries is needed to set a common strategic goal.
According to the researchers who conducted the analysis, the current system of formal and non-formal adult education in Lithuania does not ensure the provision of the necessary competencies to the industrial sector. The descriptions of employees’ qualifications validated in Lithuanian professional standards and the descriptions of vocational or study fields and programs prepared on the basis of them do not meet today’s labour market needs and future competencies related to Industry 4.0, therefore formal education cannot fully ensure future competencies. According to the legal documents, non-formal adult vocational training in Lithuania corresponds to formal learning and is unattractive for employed persons who want to improve their existing qualifications or acquire new skills necessary for the workplace.
The implementation of the apprenticeship concept in Lithuania is still rather slow, and one of the main reasons for this is the relatively low involvement and participation of employers in the implementation of apprenticeship programs. Most companies do not have the knowledge and resources to implement apprenticeship activities on their own, and educational institutions are not able to attract enough employers to agree to participate in apprenticeship programs run by educational institutions.
It is noted that the retraining measures for employees coordinated mainly by ministries are financed from the European Social Funds (ESF), therefore there is a high risk that these measures will disappear due to lack of funding after the end of the programming period and the state does not provide continuous funding. In addition, the indicators of these programs are often focused on outcome indicators rather than on the intended impact. Therefore, a sustainable and impact-oriented set of retraining measures based on sustainable financing decisions should be developed, with part of the deposit liabilities being taken over by the state.
Having assessed the ESF measures according to the amount of allocated investments, it is stated that the largest amount of funds is allocated for the acquisition or improvement of basic or low-skilled competencies, while the support for continuous improvement of high qualifications is less supported. The analysis report notes that in view of the labour market trend, where the demand for highly qualified specialists is growing and the need for low-skilled specialists is decreasing, the state’s priority should be to invest in acquiring and improving highly qualified competencies so that they can benefit from employees who are more motivated and able to create more added value.
European social fund agency
M. Katkaus str. 44, LT-09217 Vilnius
Company code: 192050725
Work hours:
I-IV 8:00-17:00 (Lunch break 12:00-12:45).
V 8:00-15:45 (Lunch break 12:00-12:45).
Phone: +370 (5) 264 9340
Email: info@esf.lt